Manufacturing: Attracting the new workforce
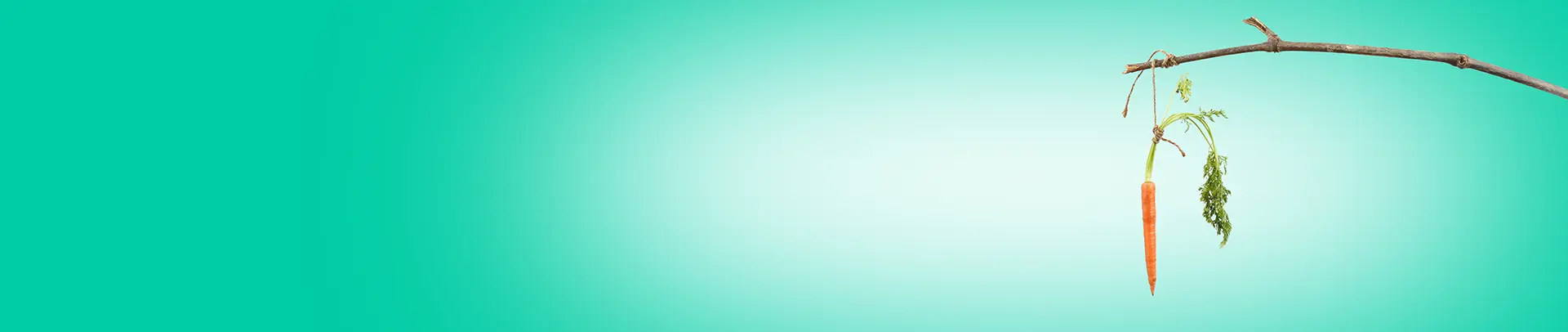
Of the many industries affected by The Great Resignation, the manufacturing industry may have been hit the hardest with a nearly 60 percent increase in resignations compared with pre-pandemic. No other industry has experienced a jump like that.
During the Great Recession, when jobs were scarce and manufacturers said they needed to cut costs to survive, workers had very little leverage. But times have changed and the last year has been a tale of worker empowerment.
Employees have figured out they’re less constrained than they thought they were in terms of where they deploy their skill sets and won’t hesitate to leave a less fulfilling job for greener pastures.
And now an industry that has quietly looked for ways to reduce labor costs in the past is now facing the challenge of not only attracting new talent but retaining their current workforce.
The new workforce
Technology advancements have helped streamline procedures, increase productivity and create a safer, more efficient workplace but have made some jobs redundant and others more complex.
Roles that were once easier to fill with rank-and-file factory workers now increasingly require digital expertise in combination with operational and procedural knowledge.
Workers who are charged with the operation and maintenance of these machines require proper training, which adds to their list of skills making them much more valuable to employers.
Luckily, the majority demographic of manufacturing workers grew up during the technological boom of the past few decades and tend to be quite adaptive to new technology.
The same majority seems to be the bulk of those driving the Great Resignation which presents a problem for hiring managers and recruiters searching for talent in this sector.
Because these roles are highly transferable, workers can take their skills to practically any company within the manufacturing sector, regardless of niche.
That’s why it’s important for companies to determine the underlying causes of turnover within their organization and the methods they use to attract new talent.
Trickle Down Culture
Anyone who’s worked in a corporate structure has probably heard of trickle-down economics: the theory that benefits for corporations and the wealthy will trickle down to everyone else.
They will also have heard other (more risqué) expressions about what else tends to roll downhill in a company.
The general takeaway is: Whatever your company culture is at the top will have effects on every other aspect of the business. That’s why some organizations rethink how they structure their hill and what to send down.
Greif, a global leader in industrial packaging manufacturing, is taking a more holistic approach to hiring and talent retention by empowering managers to make more decisions. After all, it’s the manager relationship that can retain and motivate an employee, or cause them to resign.
Greif invests in their managers by offering training in topics like diversity, neurodiverse inclusion, and unconscious bias. They also established input and feedback structures and processes designed to make all voices heard and amplify good ideas no matter where in the organization they originate.
So far, the results have been phenomenal. Hiring has increased, employee retention is up, and they now rank in the top 10 global manufacturers for employee engagement thanks to this change in company culture.
Invest to attract the best
Another timeless adage in the world of business is “you have to spend money to make money”.
Though often taken out of context by CEOs who spend money on designer office furniture and high-status credit cards, a more apt expression may be to “invest your money in places that will actually help your business grow.”
It may not roll off the tongue like its predecessor but it reminds employers that manufacturing is a growth industry and it’s important to focus your spending where it counts.
There are three key areas of investment to attract this next generation of talent:
workforce, workplace, and work experience.
Workforce
The primary cause of the high turnover rate in manufacturing is understaffing.
The misguided thought process of “more hands make less work” has led employers to drastically cut their workforce, the idea being that too many employees on hand will result in idle workers with not enough work to go around.
The reality is employers are shooting themselves in the figurative foot by leaving their remaining workers with twice the work at the same pay rate.
In order to grow in this industry, employers must realize that more hands actually produce more work.
Redundant workers protect employers from disturbances in production such as staff illnesses, vacations, sudden resignations, and other unseen circumstances.
Additionally, a full staff and flexible work schedules give employers more opportunities to train and promote from within while allowing employees the support and respite they need to avoid burnout.
Workplace
Environment plays a huge part in employee morale and overall productivity. And a little investment in this area will have huge returns.
Up-to-date equipment and software optimize your business and let your employees know you care about their work experience.
Even seemingly small physical changes to a manufacturing workplace—an updated entrance, modernized break areas, or improvements in shower and locker room facilities—can go a long way toward enhancing the employee experience.
Beyond making the workplace more comfortable it is imperative for businesses to focus on employee safety.
In the last year, social media has been flooded with videos poking fun at the various safety violations reported by workers and though initially intended to be humorous, the response from the emerging workforce has been one of indignation.
Employees will no longer tolerate cost-cutting at the expense of their safety.
Work Experience
Proper staffing and updated facilities contribute immensely to an employee’s overall experience in the workplace but what truly makes the greatest difference is the sense of respect a worker receives from their employer.
Today’s workforce isn’t satisfied feeling like a cog in a machine and employers are making big and small policy changes to ensure their staff feels like respected members of their team.
It could be something as simple as eliminating unpaid lunch breaks.
If you pay for the fuel and upkeep of your car in order for it to function properly why wouldn’t you do the same, if not more, for a human being that helps your business function?
Larger changes like establishing affinity groups within your organization, adjustments for neurodiverse employees, support for childcare, and a well-designed onboarding experience can all help build your reputation as a preferred employer.
How Leoforce can help attract the new workforce in Manufacturing
It is time for manufacturers to embrace the new workforce and understand what it takes to attract them.
With the help of Leoforce, you can find the right recipe to become an employer of choice in each community where your company has operations.
This will not only ensure that you have access to the best talent but also that you are able to build a strong reputation within your industry.